Processes
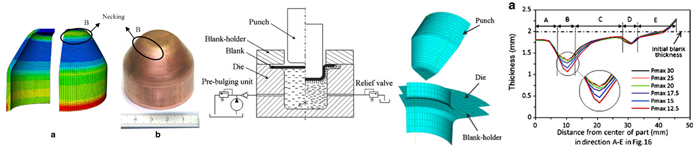
In effect, this process is used to manufacture simple or complex tubular shapes and in sheet metal forming as a substitute for deep-drawing technologies. In comparison with the conventional forming processes, the fluid replaces the force exerted by the punch, subsequently resulting in a better management of the contact problems between rigid and deformable bodies. This enables that the piece has good mechanical properties. Among hydroforming processes, we can mainly distinguish tube hydroforming and sheet or plate metal hydroforming.
At AMFRC, we investigate the effect of different characteristics process parameters on final product properties, such as impact resistance, fatigue resistance, formability, toughness, residual stress, and accumulated damage.
|
|
Investigation of hydrodynamic deep drawing for conical–cylindrical cups |
|
Gorji H., Alavi-Hashemi H., Bakhshi-Jooybari M., Nourouzi S., Hosseinipour SJ. |
|
International Journal of Advanced Manufacturing Technology, Springer |
|
Publication year: 2011 | |
|
|
Investigation of Forming Cylindrical Parts in a Modified Hydrodynamic Deep Drawing |
Assisted by Radial Pressure With Inward Flowing Liquid |
|
Yazdi MS., Bakhshi-Jooybari M., Gorji H., Shakeri M., Khademi M. |
|
Journal of Manufacturing Science and Engineering, ASME |
|
Publication year: 2018 | |
|

In bending plastic deformation occurs only in the bend region and the material away from the bend is not deformed. If the material lacks ductility, cracking may appear on the outside bend surface, but the greatest difficulty is usually to obtain an accurate and repeatable bend angle. Elastic springback is appreciable.
Various ways of bending exist such as bending a sheet in a folding machine, press brake bending in a vee-die, section of a set of rolls in a roll former, wiping down a flange, etc.
|
|
The study of spring-back of CK67 steel sheet in V-die and U-die bending processes |
|
Bakhshi-Jooybari M., Rahmani B., Daeezadeh V., Gorji H. |
|
Materials & Design, Elsevier |
|
Publication year: 2009 | |
|
|
Modeling of spring-back in V-die bending process by using fuzzy learning back- |
propagation algorithm |
|
Baseri H., Bakhshi-Jooybari M., Rahmani B. |
|
Expert Systems with Applications, Elsevier |
|
Publication year: 2011 | |
|
some of these processes are:
- Extrusion